how to reduce the corrosion of iron tip chew
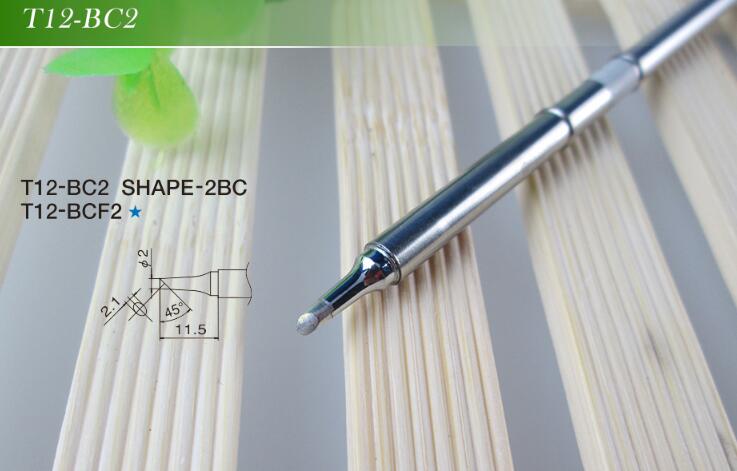
Iron chew will be slowly corroded when it's welding, T12 iron chew as a solder consumables, it is difficult to avoid corrosion, which we only ease corrosion, extend the working life. The following method is to ease the corrosion of iron chew.
1. Do not try to use non-cleaning solder paste, because non-cleaning solder paste contains acid corrosion iron chew, any kind of iron chew encounter acid, it will be subject to corrosion.
2. It should be removed the soft water ions in sponge, the ordinary water containing ions on the iron chew also corrosion.
3. Usually before welding to keep the iron chew clean, such as dirt on the iron chew surface should be promptly cleaned with a sponge, should use a special clean sponge, it will procuce corrosive substances damaged T12 tip when some sponge in the heating.
4. We should adhere to the T12 tip the most basic maintenance, including keeping the good state of absorbing tin. Although good maintenance will reduce the corrosion caused by the chemical reaction of the flux, it is also powerless to the corrosion caused by the high tin content in lead-free solder alloys.
5. It can extend the working life of iron chew if increase the thickness of the iron coating. However, this has some undesirable consequences, including reducing the thermal conductivity of the weld and the iron chew, thereby reducing the productivity of the welding operation. Thickening of the iron coating will increase the size of the head, not suitable for the fine pitch between the pins now, dense layout design and small pad size.